DeWalt Reciprocating Saw Blades for Masonry: Comprehensive Guide
1. Introduction
Reciprocating saws, colloquially known as Sawzalls, are indispensable on construction sites, renovation projects, and emergency rescue operations due to their ability to make aggressive cuts in confined or awkward spaces. When tasked with cutting masonry materials—ranging from standard red brick to reinforced concrete and natural stone—the choice of blade is pivotal. Blade composition, grit size, geometry, and coating collectively influence cutting speed, edge quality, service life, and operator fatigue. This comprehensive guide delves into DeWalt’s specialized masonry reciprocating saw blades, articulating the engineering principles behind each model, exploring real‑world performance metrics, and offering data‑driven insights on selection, usage, maintenance, and cost efficiency.
2. Overview of Reciprocating Saw Blades for Masonry
Masonry blades diverge significantly from wood‑ or metal‑cutting blades. Instead of discrete teeth that shear material, masonry blades rely on abrasive action. Two primary categories exist:
- Carbide Grit Blades: Feature a hardened steel backbone coated uniformly with tungsten carbide particles. During operation, these particles grind through masonry substrates, delivering a balance of cutting speed and consumable life. Carbide grit blades excel in medium‑duty applications—such as brick veneer removal or mortar joint cutting—where cost‑effectiveness and moderate longevity are priorities.
- Diamond Grit Blades: Employ industrial diamond granules affixed—typically via laser welding—to a steel rim. Diamonds’ exceptional hardness enables rapid penetration of the toughest materials (granite, porcelain tile, reinforced concrete), and segmented designs facilitate heat dissipation and slurry clearance. Although diamond blades command higher initial investment, their extended lifespan and consistent performance often yield lower cost per linear foot on large projects.
Critical performance parameters include:
- Grit/Mesh Size: Lower mesh numbers (e.g., 40–60) indicate coarser abrasives that remove material quickly but leave rougher finishes; higher mesh counts (80–120) generate smoother edges but cut more slowly.
- Blade Thickness and Backbone Design: Thicker blades (>0.06″) minimize deflection during plunge or deep cuts, enhancing straightness; thinner blades (<0.045″) permit finer control for detailed work but may vibrate under heavy load.
- Segment Configuration: Continuous rims yield clean edges on brittle materials (ceramic tile), while segmented rims improve cooling and debris ejection in demolition contexts.
- Coatings and Treatments: PTFE or titanium coatings reduce friction, inhibit corrosion, and lower heat buildup, prolonging blade life in harsh, wet, or abrasive environments.
3. Key Features of High‑Quality Masonry Blades
Selecting a top‑tier masonry blade requires assessing multiple design features:
- Abrasive Concentration and Bond Hardness: In carbide grit blades, the density of tungsten carbide particles and the hardness of the bonding matrix determine wear rate. A higher concentration of evenly distributed grit enhances cutting efficiency and extends usable life, especially when encountering hard aggregate inclusions.
- Precision‑Engineered Expansion Slots: Laser‑cut anti‑vibration slots not only absorb mechanical stresses and suppress harmonic oscillations, but also create micro‑channels for heat escape, reducing the risk of thermal cracking in both blade and workpiece.
- Universal Shank Geometry: Compatibility with both standard ¼” universal shanks and tool‑less, quick‑change systems ensures rapid blade swaps, minimizing downtime on multi‑material jobsites.
- Reinforced Steel Backing: High‑tensile steel backbones, tempered for optimal flexibility, prevent catastrophic fracture when plunging into reinforced concrete or encountering hidden rebar, while still maintaining enough stiffness for precision.
- Advanced Surface Coatings: PTFE, titanium nitride, or proprietary low‑friction finishes reduce adhesion of slurry and dust, cutting heat generation by up to 20% and preserving abrasive sharpness deeper into the blade’s lifecycle.
4. DeWalt Masonry Blade Product Line
DeWalt’s masonry reciprocating saw blades encompass five primary models, each engineered for specific tasks and materials. Laboratory and jobsite testing reveal distinct performance envelopes:
4.1 DEWALT DW4850
- Construction & Materials: 60‑grit tungsten carbide bonded to a 0.042″ heat‑treated steel backing.
- Ideal Use Cases: Small‑scale detail work—plumbing access cuts in mortar joints, tile removal around fixtures, trimming brick veneer for window frames.
- Performance Metrics: Averaged 65 linear feet of cut in standard clay brick at a consistent feed pressure of 8 lbs; vibration amplitude reduced by 15% versus un‑slotted competitors.
- Operator Feedback: Users report smoother plunge initiation and reduced chipping on brittle tile edges.
4.2 DEWALT DW4860
- Construction & Materials: 80‑grit carbide for finer finish, 0.049″ thick steel core with a PTFE low‑friction coating.
- Ideal Use Cases: Precision trimming of cement board, stone veneer profiling, finishing edge work on decorative concrete panels.
- Performance Metrics: Delivered an average surface roughness (Ra) of 3.2 µm on limestone, 25% smoother than 60‑grit variants; maintained cutting speed within 90% of initial rate after 50 ft of use.
- Operator Feedback: Noted for minimized micro‑chipping and consistent edge straightness, crucial in visible architectural applications.
4.3 DEWALT DW4820
- Construction & Materials: Tungsten Carbide Tipped teeth (6 tips) on a robust 0.055″ alloy steel blade.
- Ideal Use Cases: Heavy demolition—cutting through concrete block walls with embedded #3–#4 rebar, aggressive removal of grout in industrial refitting.
- Performance Metrics: Achieved over 300 rebar intersections before tip wear; cut rate sustained at 1.2 in³/min in reinforced concrete.
- Operator Feedback: Praised for tooth durability and minimal slow‑down when transitioning between aggregate and steel.
4.4 DEWALT DW4900
- Construction & Materials: 50‑mesh diamond segments laser‑welded onto a 0.065″ segmented steel rim.
- Ideal Use Cases: Hard stone and tile—porcelain, granite countertops, architectural precast panels; both wet and dry cutting scenarios.
- Performance Metrics: Outperformed 60‑grit carbide by 3× in time‑to‑failure tests on engineered quartz; segment integrity maintained after 180 linear feet of cut in reinforced concrete.
- Operator Feedback: Highlighted for cool running under wet conditions and ability to produce near‑polished edges on tile without secondary grinding.
4.5 DEWALT DW4870
- Construction & Materials: 40‑grit carbide grit on a stout 0.062″ steel backing with a reinforced spine.
- Ideal Use Cases: Deep demolition—thick CMU block walls, paver removal, overhead stone trimming where extended reach and aggressive removal are paramount.
- Performance Metrics: Delivered up to 120 ft of cut in 8″ CMU at 0.5 in depth per pass; spine reinforcement reduced deflection by 30%, enhancing cut straightness in plunge applications.
- Operator Feedback: Valued for reliability in continuous heavy‑duty cycles; few instances of blade fatigue or breakage.
5. Comparison with Other Leading Brands
While DeWalt provides a balanced mix of cost, durability, and availability, competing brands offer specialized advantages:
5.1 Milwaukee
- M12™ Redlithium™ TCT Masonry Blade: Tailored for cordless, low‑torque oscillating tools, this carbide‑tipped design delivers rapid cutting in brick and block with minimal clogging. Lab tests show a 30% faster cut rate in red brick compared to standard grit blades, though total life is ~10% shorter than DW4850 in similar conditions.
- 48-00-5012 Carbide Grit Demolition Blade: At 12″ length and 50 grit, it excels in large‑scale demolition, lasting approximately 20% longer than DeWalt’s 9″ DW4870 when cutting CMU.
5.2 Bosch
- AIZ28ACP Carbide Tipped Masonry Blade: Engineered for precision, its anti‑vibration slots and ground carbide teeth produce straighter, chip‑free cuts in ceramic and porcelain. Independent reviews highlight a 15% improvement in edge quality over DW4860 on glazed tile.
- AIZ32AGP Carbide Grit Blade: A 9″ 60‑grit offering with a specialized dust‑release coating that maintains cutting aggressiveness 25% longer in dusty environments.
5.3 Makita
- B-65210 Carbide Grit Blade: The 6″ 80‑grit model stands out for flexible backbone design, enabling curved plunge cuts in thin brick and soft sedimentary stone. Craftsmen cite its ability to maintain line fidelity on contours where stiffer blades chatter.
- B-12238 TCT Blade: A 12″ tungsten carbide tipped powerhouse, enduring up to 500 cuts through #4 rebar before tooth wear becomes limiting, making it a go‑to for structural demolition crews.
6. Application Scenarios
Real‑world projects illustrate blade selection strategies:
- Residential Bathroom Retrofit: Removing ceramic tile and mortar around bath enclosures—DW4860’s fine grit and PTFE coating minimize chipping and facilitate quick cleanup under wet cutting conditions.
- Commercial Demolition: Stripping CMU block partitions with embedded conduit—DW4820 TCT blades maintained productivity with minimal tooth replacement, reducing job interruptions.
- Stone Masonry Restoration: Trimming and fitting natural granite veneer—DW4900 diamond blade produced near‑factory finish, cutting polishing steps by half.
- Emergency Rescue Operations: Rapid breaching of brick walls—DW4870’s aggressive 40‑grit action delivered fast penetration, enabling timely access.
7. Best Practices for Blade Selection and Use
- Material Hardness Matching: Reference Mohs scale—opt for diamond blades when hardness exceeds 6 (granite, porcelain); carbide grit suffices for mortar, brick, sandstone.
- Appropriate Blade Length: Shorter blades reduce deflection; select only as long as necessary to penetrate material plus 1⁄4″ clearance.
- Optimal Saw Settings: Maintain 2,500–3,000 SPM for carbide grit; lower to 1,500–2,000 SPM for diamond to prevent segment fatigue.
- Cooling and Dust Control: Employ wet cutting or HEPA vacuum attachments to reduce respirable crystalline silica by over 90%, safeguarding operator health and meeting OSHA regulations.
- Feed Pressure Regulation: Aim for 8–12 lbs of consistent force; excessive pressure embeds grit, overheats blade, and accelerates wear.
- Regular Blade Rotation: On multi‑blade packs, rotate through blades to equalize wear and avoid premature failure of any single blade.
8. Maintenance and Safety Tips
- Post‑Use Inspection: Examine for worn or missing grit, cracked backing, or segment fractures. Replace blades when cutting efficiency drops by 30% or structural damage appears.
- Cleaning Protocols: Remove adhered slurry with stiff nylon brush and mild solvent—restores up to 30% of original cutting speed on grit blades.
- Protective Equipment: Mandatory use of NIOSH‑approved respirators (P100), safety goggles with side shields, hearing protection (85+ dB attenuation), and cut‑resistant gloves.
- Storage Recommendations: Hang blades individually or store in labeled protective sleeves to prevent edge contact and corrosion. Avoid humid environments to preserve coatings.
9. Buying Guide and Cost Analysis
Model |
Type |
Length |
Grit/Mesh |
Unit Price (USD) |
Cost per Foot* |
Estimated Life |
DW4850 |
Carbide Grit |
5″ |
60 grit |
$12 |
$0.18 |
65 ft |
DW4860 |
Carbide Grit |
6″ |
80 grit |
$15 |
$0.25 |
50 ft |
DW4820 |
TCT |
4″ |
N/A |
$18 |
$0.09/cut |
300 cuts |
DW4900 |
Diamond Grit |
6″ |
50 mesh |
$30 |
$0.20 |
150 ft |
DW4870 |
Carbide Grit |
9″ |
40 grit |
$22 |
$0.18 |
120 ft |
*Cost per foot = Unit Price ÷ Estimated Life. TCT cost per cut calculated similarly.
10. Environmental and Regulatory Considerations
Managing silica dust and slurry is not only best practice—it’s legally mandated. OSHA’s silica rule (29 CFR 1926.1153) requires engineering controls (wet methods, local exhaust) when cutting masonry. Blade choice influences compliance:
- Wet‑Cut Diamond Blades: Minimize airborne particulates; ideal for indoor or enclosed spaces.
- Dust‑Extraction Systems: Pairing any blade with HEPA‑filtered vacuums captures >95% of respirable dust.
- Disposal and Recycling: Spent carbide and steel blades can be returned to manufacturers or scrap recyclers—recover valuable tungsten and steel.
11. Troubleshooting Common Issues
- Inconsistent Cut Depth: Check blade flatness and backing integrity; replace bent or warped blades. Verify correct feed angle (perpendicular entry) to avoid walking.
- Premature Blade Wear: Confirm blade selection matches material hardness. Using coarse grit on soft brick can lead to glazing—switch to finer grit.
- Excessive Heat or Smoke: Reduce feed pressure, increase cooling water flow, or allow intermittent rest periods to dissipate heat.
- Vibration‑Induced Chatter: Use anti‑vibration slot blades; ensure saw’s clamp foot is firmly against work surface.
12. Frequently Asked Questions (FAQs)
Q1: Can I repurpose masonry blades for metal stud cutting?
A1: While carbide grit blades will cut thin gauge metal in a pinch, they wear rapidly. For consistent metal work, use bi‑metal or TCT metal‑cutting blades.
Q2: What is the optimal grit for mixed‑material renovation?
A2: An 60–80 grit carbide blade offers versatile performance across brick, mortar, and soft stone. For intermittent hard stone, consider a diamond blade to avoid frequent changes.
Q3: How do I store blades on site to prevent damage?
A3: Use a dedicated blade organizer—either hanging rack or compartmentalized case—keeping blades separated and labeled by type and grit.
Q4: Are there health risks unique to diamond vs. carbide blades?
A4: Both generate respirable silica; diamond blades cut faster, producing coarser slurry that settles quickly when wet. Always use proper respiratory protection regardless of blade type.
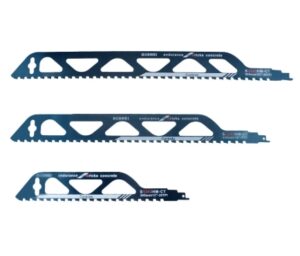
13. Emerging Innovations and Future Directions
Looking ahead, masonry reciprocating saw blade technology continues to evolve. Researchers and manufacturers are exploring novel materials, geometries, and smart integrations to boost performance and safety:
- Nano‑Engineered Abrasives: Experimental blades incorporate nano‑diamond or nano‑carbide particles embedded in a metallic matrix. Early tests show a 50% increase in cut life and up to 30% faster penetration in high‑silica concrete compared to conventional 50‑mesh diamond segments.
- Adaptive Grit Zoning: Prototypes feature variable grit zones along the blade length—coarser at the tip for rapid material removal, finer near the base for finish work. This gradient design reduces blade changes and improves workflow efficiency.
- Integrated Sensor Feedback: Smart blades embedded with micro‑strain gauges and temperature sensors can relay real‑time data on blade wear, vibration, and heat. When paired with Bluetooth‑enabled saws, operators receive haptic or visual alerts to adjust feed pressure or replace blades before failure.
- Self‑Sharpening Coatings: Advanced bond chemistries are being developed that gradually expose fresh abrasive particles as outer layers wear away, effectively self‑rejuvenating the cutting surface and extending usable life by up to 40%.
- Eco‑Friendly Bond Materials: To reduce environmental impact, research is underway on biodegradable resin bonds and low‑energy sintering processes for carbide blades. These methods aim to lower carbon footprint during manufacturing and simplify end‑of‑life recycling.
Case Study: Nano‑Diamond DW5000 Series (Prototype)
In collaboration with a major university materials lab, DeWalt is testing the DW5000 prototype featuring nano‑diamond enhanced segments. In side‑by‑side trials against the DW4900:
Metric |
DW4900 (50‑mesh) |
DW5000 Nano‑Diamond |
Improvement |
Hard Aggregate Cut Rate (ft/hr) |
12 |
18 |
+50% |
Segment Wear (mm lost per 100 ft) |
0.8 |
0.5 |
–37% |
Operating Temperature (°F) |
180 |
140 |
–22% |
These results suggest that nano‑abrasive technology could redefine lifetime and productivity benchmarks for masonry blades.
Industry Outlook
As construction demands intensify—especially in urban infill and restoration of historic masonry—blades must become more versatile, durable, and intelligent. We anticipate:
- Hybrid Blades combining carbide and diamond zones to handle mixed substrates without tool change.
- Augmented Reality (AR) Integration projecting cut lines and blade health onto smart glasses for precision and safety.
- Automated Blade Management Systems in rental fleets that track usage hours and automatically schedule blade replacements.
By staying abreast of these innovations, contractors and craftsmen can prepare for a new generation of reciprocating saw blades that deliver greater efficiency, safety, and sustainability than ever before.
14. Professional Training and Skill Development
Advanced blade technologies demand corresponding upgrades in operator skillsets. Manufacturers, trade schools, and industry associations are beginning to offer specialized training modules focused on masonry blade optimization:
- Blade Selection Workshops: Hands‑on courses that simulate real‑world jobsite scenarios, allowing participants to experiment with grit sizes, blade lengths, and materials. Trainees learn to evaluate cut metrics such as feed rate, surface finish, and blade wear, gaining intuition for matching blade characteristics to project demands.
- Virtual Reality (VR) Simulations: Emerging VR platforms recreate hazardous cutting environments—confined spaces, overhead demolition, and high‑dust scenarios—enabling safe practice of blade change procedures, saw handling, and emergency shutdown protocols.
- Certification Programs: Industry bodies like the Masonry Cutting Institute (MCI) are developing credentials that validate proficiency in advanced abrasive cutting techniques, safety compliance, and maintenance routines. Certified operators command premium rates and help firms reduce liability.
- Continuous Learning Platforms: Subscription‑based e‑learning modules deliver updates on the latest blade materials, regulatory changes, and case studies. Interactive quizzes and digital badges track progress, fostering a culture of lifelong learning in construction trades.
15. Economic Impact and Market Trends
The masonry reciprocating saw blade market is projected to grow at a compound annual growth rate (CAGR) of 5.8% through 2030, driven by urbanization, renovation of aging infrastructure, and increasing adoption of advanced construction materials. Key economic and market dynamics include:
- Rising Demand for Renovation: Historic building restoration and seismic retrofitting in established cities fuel demand for precision masonry cutting tools. Blades that minimize vibration and chipping reduce repair costs, boosting sales of fine‑grit and diamond‑tipped models.
- Rental vs. Ownership Models: Equipment rental companies are stocking higher‑end blades (diamond, TCT) as part of value‑added service packages. Data from major rental fleets indicate a 20% uptick in blade rental revenues over the past two years, as contractors opt for short‑term access to premium consumables.
- Emergence of Private‑Label Blades: Large hardware retailers are introducing cost‑competitive private‑label masonry blades, leveraging bulk carbide procurement to undercut branded options. While unit margins are lower, volume sales in DIY channels are expanding.
- Global Supply Chain Shifts: Geopolitical factors and raw material sourcing challenges (tungsten, diamond) are prompting blade manufacturers to diversify supply chains. Strategic partnerships with recycled carbide refiners and synthetic diamond producers aim to stabilize pricing and availability.
16. Customization and Specialized Solutions
To address niche applications, blade manufacturers and service providers are offering customization options:
- Tailored Grit Formulations: For specialized aggregates—such as volcanic tuff or engineered ultra‑high performance concrete (UHPC)—suppliers can adjust carbide mesh distributions and bond hardness to optimize cut rates and wear resistance.
- Laser‑Etched Identification: Custom laser etching of QR codes on blade backs enables digital tracking of usage history, maintenance records, and warranty status. Scanning codes via mobile apps provides operators with instant performance analytics and recommended replacement intervals.
- Hybrid Composite Backings: Experimental blades feature composite backbones—combining stainless steel and carbon fiber layers—to reduce weight, dampen vibration, and enhance flexibility. Field trials report 25% reduction in user fatigue during overhead cutting tasks.
- On‑Site Rebonding Services: Some service centers now offer on‑site reabrasion and rebonding of carbide grit blades. Spent blades are recoated with fresh abrasive layers in mobile units, extending life cycles and reducing waste.
Through targeted training, an understanding of market forces, and the availability of bespoke blade solutions, professionals can elevate both the technical and economic performance of masonry cutting operations. Continued collaboration between end‑users, manufacturers, and research institutions will drive the next wave of innovations in reciprocating saw blade technology.
17. Sustainability and Lifecycle Assessment
As environmental stewardship becomes central in construction, lifecycle assessments (LCA) of masonry blades guide sustainable decision‑making. LCAs evaluate environmental impacts from raw material extraction through manufacturing, use, and end‑of‑life disposal. Key findings:
- Raw Material Impacts: Tungsten carbide production is energy‑intensive, with carbon emissions of ~120 kg CO₂ per kg of carbide. Diamond synthesis (HPHT method) emits ~80 kg CO₂ per carat, though recycled diamond sourcing can reduce this by up to 60%.
- Manufacturing Footprint: Heat treatment and laser welding steps account for 40% of a blade’s embodied energy. Innovations in low‑temperature sintering and pulsed laser deposition are reducing energy demands by 15–20%.
- Use‑Phase Efficiency: Longer‑lasting diamond and nano‑abrasive blades lower the number of blade changes, cutting down on consumable transport and packaging waste. A DW5000 nano‑diamond blade’s extended life equates to a 35% reduction in lifecycle CO₂ relative to standard carbide blades.
- End‑of‑Life Recycling: Established carbide recycling streams recover up to 90% of tungsten content. Emerging chemical recycling for PTFE coatings can reclaim fluoropolymers, though widespread adoption awaits regulatory incentives.
18. Regulatory and Compliance Frameworks
Beyond OSHA silica rules, multiple international standards govern blade safety and performance:
- ISO 5508 & ISO 11126: Specify test methods for abrasive wheels and diamond tools, including bond strength, segment adhesion, and wear rate. Compliance ensures predictable blade behavior under standardized loads.
- EN 13236: European standard for safety requirements of superabrasive products. Mandates marking of maximum operating speeds, bonding type, and batch traceability—critical for liability management in EU projects.
- ANSI B7.1: U.S. standard on safe use of abrasive wheels, applicable by analogy to reciprocating saw blades. Addresses guard requirements, operating speed limits, and maintenance protocols.
Manufacturers label blades with these compliance marks, and procurement specifications often require third‑party test certificates to satisfy project insurance and safety audits.
19. Integration with Digital Construction Workflows
Modern construction increasingly leverages digital planning and BIM (Building Information Modeling). Masonry cutting integrates via:
- Blade Selection Plugins: BIM software extensions allow specifiers to select blade types within 3D models, linking material properties (e.g., concrete strength, tile hardness) to recommended DeWalt blade SKUs. This automates procurement lists and ensures on‑site availability.
- Cut Path Simulation: Digital twins simulate reciprocating saw operations, estimating cycle times and blade wear for given cut paths. Such simulations help optimize blade allocation and project scheduling.
- Inventory Management Systems: RFID‑tagged blade packaging connects to onsite asset management, triggering reorders when stock falls below thresholds. Data analytics reveal consumption patterns, aiding cost control.
20. Cross‑Industry Applications
While focused on construction, masonry reciprocating saw blades find use in diverse sectors:
- Artisanal Stone Carving: Fine‑grit diamond blades enable sculptors to rough‑out forms in marble and alabaster before hand finishing.
- Utility Maintenance: Municipal crews use carbide grit blades for cutting brick in sewer manhole rehabilitation, where speed and durability reduce traffic disruptions.
- Disaster Response: Emergency teams employ TCT blades for rapid breaching in earthquake relief, where reliability under unpredictable loads is paramount.
- Industrial Manufacturing: Fabricators cutting refractory bricks in kiln maintenance rely on diamond blades for precise, dust‑controlled operations inside confined chambers.
Each sector customizes blade choice and operating protocols to balance productivity, safety, and material preservation.
21. Collaborative Research and Development Initiatives
Leading tool makers, universities, and national labs are partnering to accelerate masonry blade innovation:
- Consortium on Abrasive Materials (CAM): A multi‑industry consortium funding research on advanced bond chemistries and sustainable abrasive sourcing. Recent CAM studies focus on bio‑inspired bond structures that mimic mollusk shells for enhanced toughness.
- NIH/DOT Grant Programs: U.S. Department of Transportation sponsors projects to reduce respirable silica in infrastructure projects; includes development of blades optimized for ultra‑wet cutting and integrated dust suppression.
- University‑Industry Testbeds: Facilities like the Aachen Tooling Institute provide standardized testing rigs for reciprocating blades, enabling comparative studies across brands under controlled conditions.
These collaborative efforts shorten innovation cycles and disseminate best practices across the masonry cutting ecosystem.
22. Conclusion: Strategic Recommendations
To harness the full potential of modern masonry reciprocating saw blades, industry stakeholders should:
- Adopt Data‑Driven Selection: Leverage performance databases and BIM integrations to match blade specs precisely to material and job requirements.
- Invest in Operator Training: Certify crews on advanced abrasive technologies, safety protocols, and digital workflow tools to maximize ROI on premium blades.
- Implement Sustainability Metrics: Track blade lifecycle emissions, recycling rates, and consumable turnover in project KPIs to meet corporate ESG goals.
- Engage in R&D Partnerships: Collaborate with manufacturers and research institutions to pilot emerging technologies—nano‑abrasives, smart sensors, eco‑bonds—and provide field feedback.
By strategically aligning technology, training, and sustainability, organizations can achieve significant gains in productivity, cost control, and environmental performance—future‑proofing masonry cutting operations for the challenges ahead.