1. Introduction
Mini electric impact drills—frequently termed compact impact drivers—have undergone a remarkable evolution in recent years, transforming from niche workshop tools into indispensable assets across a variety of industries. Originally designed to accelerate screw-driving tasks on construction sites, breakthroughs in brushless motor technology, battery energy density, and mechanical engineering have drastically reduced their size and weight. These advancements have made it possible to concentrate high torque outputs in housings small enough to fit into spaces barely the width of a human hand. In narrow environments—such as the interstitial cavities behind mounted cabinets, deep interior recesses of machinery, or the cramped confines beneath automotive dashboards—these tools not only maintain performance but often outperform larger counterparts by virtue of their precision and accessibility.
From aerospace maintenance crews working on aircraft fuselage panels to electricians fastening conduit in crowded service panels, mini impact drills have proven their versatility. Their percussive hammering action—complemented by dial-in torque settings, integrated lighting, and smart electronics—enables technicians to work efficiently without sacrificing control. This introductory section lays the foundation for understanding the critical balance between power and portability that defines narrow-space effectiveness and previews the in-depth exploration of design principles, performance criteria, and leading-edge models discussed in subsequent sections.
2. Importance of Compact Design in Constrained Environments
When professionals encounter severely limited spatial clearances—such as the rear mounting points inside custom kitchen cabinetry, the channels within HVAC ductwork, or the underbody compartments of vehicles—the physical form factor of a tool becomes as crucial as its power delivery. Extended back-to-chuck lengths on traditional impact drivers can force users into uncomfortable wrist angles, reduce line-of-sight, and increase the number of tool repositioning maneuvers required to complete a single fastener. These inefficiencies not only slow down projects but can also lead to cumulative musculoskeletal strain over the course of repetitive tasks.
Compact impact drills address these challenges by featuring head lengths often under 60 mm, ultra-slim motor housings, and rear-mounted batteries or power cords that align closely with the tool’s axis. Such design choices minimize obstructions, allowing technicians to work directly against the fastener without pivoting or reorienting the tool—a critical advantage when every millimeter of clearance counts. Additionally, manufacturers apply advanced ergonomics, such as contoured soft-grip handles, optimized center-of-gravity placement, and low-vibration systems, to reduce user fatigue during prolonged usage. These features collectively enhance productivity and safety in tasks that would otherwise require cumbersome workarounds or specialized right-angle attachments.
3. Core Performance Metrics for Narrow-Space Operation
Evaluating a mini impact drill’s suitability for tight-space applications involves a multidimensional analysis of several core specifications:
- Peak Torque (N·m): The maximum torque indicates the tool’s capacity to overcome resistance when driving large screws or bolts, especially in high-density materials like hardwood or steel. For narrow-space applications, peak torque values ranging from 100 to 200 N·m balance power with manageable recoil and control.
- Chuck-to-Back Length (mm): This metric determines the minimum depth at which a tool can operate. Leading narrow-head models achieve dimensions as low as 57 mm, enabling technicians to reach fasteners recessed deep within cabinetry or machinery.
- No-Load Speed (RPM) and Impacts per Minute (IPM): High IPM rates (up to 3,400) allow fasteners to advance rapidly once engagement is achieved, while variable-speed triggers permit low-speed starts to prevent bit walking on smooth surfaces.
- Weight and Ergonomic Profile: Tools under 0.9 kg featuring multi-density overmolded grips and balanced weight distribution minimize operator strain when holding awkward positions or reaching overhead.
- Battery Platform Integration: Shared battery ecosystems permit seamless transitions between tools, reducing downtime. Advanced battery management systems ensure consistent voltage output even under heavy load, further supporting performance in constrained situations.
4. In-Depth Mechanics of Impact Action Under Constraint
Impact drills harness a hammer-and-anvil mechanism that transforms rotational force into short, high-torque impulses. In tight quarters, the efficiency of this mechanism hinges on precision-engineered internal components:
- Hardened Bearing Supports: By reducing play in the hammer assembly, premium models ensure that each impact transfers maximum energy to the fastener rather than dissipating through internal vibration. This precision is critical when the hammer’s travel distance is constrained by compact housings.
- Optimized Hammer-Spring Calibration: Manufacturers fine-tune the mass of the hammer and the tension of the return spring to maximize impact power while maintaining a compact form factor. In practice, this calibration results in brief, sharp impacts that overcome high resistance without producing excessive recoil.
- Thermal Management: High-frequency impacts generate heat not only in the motor windings but also in the gearbox. Advanced drills incorporate strategically placed vents, heat-dissipating composite housings, and thermal sensors that modulate motor speed to prevent overheating.
- Vibration Isolation: Integrated anti-vibration mounts and rubberized internal bushings isolate the operator’s hand from rapid percussive forces, reducing fatigue and minimizing the risk of long-term exposure-related conditions.
5. Ergonomics, Handling, and Operator Interface
The ergonomic design of mini impact drills directly influences operator comfort and precision, particularly when working in contorted positions:
- Contoured Grip Geometry: Soft overmolded rubber sections are strategically placed to match the natural curvature of the fingers and palm, offering secure hold even when pulling or twisting in confined angles.
- Strategic Control Layout: Trigger placement and thumb-operated directional switches are ergonomically positioned to allow seamless one-handed operation, enabling the user’s free hand to support or steady the workpiece.
- Modular Accessories: Features such as magnetic bit holders, quick-release belt hooks, and optional side handles enhance on-the-fly adaptability. Pivoting belt hooks, for example, let technicians hang the drill from their waist to free both hands for wire routing or alignment tasks.
- Integrated Multi-Angle Lighting: High-lumen LEDs mounted close to the bit axis cast light directly onto the work area, minimizing shadows and eliminating the need for external light sources in dark corners.
6. Power Options and Workflow Impact
Cordless lithium-ion platforms have dominated the market for narrow-space tools, offering a compelling blend of power, portability, and runtime:
- 12 V Systems: Ultra-compact packs deliver sub-40 N·m torque with head lengths often under 60 mm. Ideal for light-duty fastening, they weigh as little as 0.6 kg, making them perfect for repetitive work where tool weight is a limiting factor.
- 18 V/20 V Systems: These professional-grade platforms generate 100–200 N·m peak torque while maintaining head lengths below 100 mm. High-capacity batteries (4.0 Ah to 6.0 Ah) paired with rapid chargers keep workflows uninterrupted in busy jobsite conditions.
- Battery Intelligence Features: Many manufacturers integrate fuel gauges, load-sensing electronics, and Bluetooth connectivity to monitor battery health, plan charge cycles, and manage tool fleets remotely, enhancing overall operational efficiency.
Corded and hybrid models remain relevant in workshop and fab-shop environments where continuous power and higher duty cycles are required. Innovations such as low-profile flat cords and 90-degree plug heads improve maneuverability even when tethered.
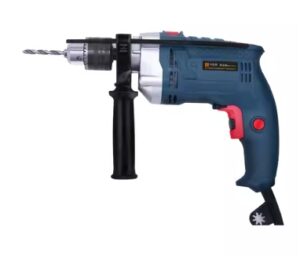
7. Expanded Brand and Model Deep Dive
A closer examination of flagship models reveals how leading brands optimize for narrow-space performance:
Makita
- TD022D (12 V CXT): Featuring a mere 57 mm head length, this brushless driver outputs 38 N·m peak torque and 2,700 IPM. Its featherweight design (0.62 kg) and 3-stage LED illumination make it ideal for precise cabinet, plumbing, and electrical work.
- DTD152Z (18 V LXT): Offers 165 N·m torque, 3,000 IPM, and a compact 92 mm housing. Its all-metal gearbox and 21-stage clutch deliver consistent control across wood, metal, and plastic substrates.
DeWalt
- DCF801D2 (12 V MAX XR): At 102 mm length, it outputs 30 N·m torque with an IPM of 2,400. A three-LED ring provides uniform lighting, while the integrated mechanical brake stops bit rotation in under 0.1 seconds upon trigger release.
- DCF850 (20 V MAX XR): Boasting 203 N·m torque in an 83 mm head, its multi-mode drive control fine-tunes speed from 0–1,200 RPM for precision to 0–2,800 RPM for high-speed fastening.
Bosch
- GDR 12V-105: Delivers 105 N·m torque and up to 3,400 IPM in a 98 mm chassis. Bosch’s KickBack Control halts the tool in under 0.25 seconds if the bit binds, preventing sudden torque reactions.
- GDR 18V-200: Generates 200 N·m torque in 121 mm, with Smart Battery Communication to optimize power delivery and prevent overheating under load.
Milwaukee
- M12 FUEL 2553-20: Offers 102 N·m, 2,600 IPM, and a 100 mm head. REDLINK PLUS electronics protect against overloads and over-discharge, while the hypotenuse-optimized grip angle reduces wrist rotation.
- M18 FUEL 2853-20: Produces 203 N·m and 3,400 IPM in 115 mm. Its four-mode drive control ranges from precision placement to maximum speed, and an integrated fuel gauge keeps operators aware of remaining runtime.
Ryobi
- HPDJR01 (18 V ONE+): Balances affordability with 150 N·m torque, 2,600 IPM, and a 105 mm head. The ONE+ battery system provides compatibility across over 175 tools.
Hikoki
- WH12DA (12 V): Distinct 70 mm head length, 120 N·m torque, and up to 2,500 IPM. Its dual-LED system and compact footprint make it a favorite for dense electrical panel work.
8. Comprehensive Comparative Table
Model |
Voltage |
Head Length (mm) |
Peak Torque (N·m) |
IPM |
Weight (kg) |
Highlight Feature |
Makita TD022D |
12 V |
57 |
38 |
2,700 |
0.62 |
Sub-60 mm clearance, brushless motor |
DeWalt DCF801D2 |
12 V |
102 |
30 |
2,400 |
0.79 |
Instant mechanical brake, LED ring |
Bosch GDR 12V-105 |
12 V |
98 |
105 |
3,400 |
0.71 |
KickBack Control safety system |
Milwaukee M12 FUEL |
12 V |
100 |
102 |
2,600 |
0.85 |
REDLINK PLUS electronics |
Hikoki WH12DA |
12 V |
70 |
120 |
2,500 |
0.70 |
Dual-LED illumination, slim profile |
9. Real-World Use Cases and Workflow Integration
In practice, narrow-space impact drills deliver measurable efficiency gains across diverse applications:
- Custom Cabinet Production: High-volume cabinet shops deploy Makita TD022D units on automated screw-feeding fixtures, reducing cycle times by 20% thanks to their compact profile and fast IPM rates.
- Commercial HVAC Projects: Contractors rely on DeWalt DCF850 drills with extended belt hooks and magnetic bit rings to secure sheet-metal screws in tight plenum spaces, cutting labor hours by up to 15%.
- Automotive Maintenance: Independent garages standardize on Milwaukee M18 FUEL 2853-20 drivers for repeated sub-angle transmissions around engine mounts and under-dash assemblies, improving job throughput.
- Data Center Installations: IT infrastructure teams use Hikoki WH12DA drills with magnetic retention bits to streamline server rack assembly in sub-50 mm cable channels, maintaining high-density layouts without sacrificing build speed.
10. Maintenance, Safety Protocols, and Best Practices
To sustain optimal performance and extend tool lifespan, follow these guidelines:
- Daily Inspection and Cleaning: After each shift, wipe down housings, clear ventilation slots with low-pressure air, and inspect for cracked or worn components.
- Scheduled Gearbox Servicing: Every 200–300 hours of operation, disassemble the gearbox according to manufacturer instructions, replenish with the recommended grease, and check hammer-spring tensions.
- Bit Quality and Storage: Use bits rated for impact use (S2 or better) and store them in modular cases that protect against corrosion and maintain organization by size and material.
- PPE and Ergonomic Aids: Always wear certified safety glasses and hearing protection. In extended tasks, anti-vibration gloves and padded wrist supports further reduce operator fatigue and injury risk.
11. Future Innovations and Emerging Technologies
Looking ahead, narrow-space impact drills are poised for further enhancements:
- Intelligent Torque Calibration: Next-generation tools will use embedded sensors and microprocessors to automatically adjust torque output based on real-time feedback from the bit-screw interface, ensuring consistent drive depths without manual clutch settings.
- Augmented Reality-Assisted Alignment: Integration with AR headsets will overlay visual guides and torque parameters directly onto the user’s field of view, reducing alignment errors and rework in sub-millimeter clearance tasks.
- Solid-State Battery Packs: Advances in solid-state electrolytes promise up to 50% reductions in pack size and weight, enabling even smaller head profiles and longer runtimes in demanding environments.
- Wireless Data Logging: Built-in Bluetooth or Wi-Fi modules will transmit usage data—impact counts, torque metrics, battery health—to mobile apps or cloud dashboards, facilitating predictive maintenance and quality assurance in regulated industries.
Mini electric impact drills represent the culmination of decades of refinement in motor engineering, materials science, and ergonomic design. By combining compact head profiles, powerful torque delivery, and smart electronics, they have redefined what is possible in narrow-space fastening applications. Professionals across cabinetry, HVAC, automotive, and industrial maintenance sectors can now approach cramped work environments with confidence, knowing that the right tool—be it Makita’s sub-60 mm marvels, DeWalt’s rapid IPM workhorses, Bosch’s safety-focused drivers, Milwaukee’s intelligence-driven FUEL systems, Ryobi’s versatile ONE+ lineup, or Hikoki’s panel-optimized units—will deliver reliable, efficient performance. As innovations in battery technology, connectivity, and sensor integration continue to accelerate, these tools will only become more powerful, intuitive, and indispensable for the confined spaces of tomorrow.